Sacred Commitment to Health and Safety Lessons from Millikens Safety Way
- About Us
-
Businesses
-
Main Menu
- Businesses
- Our Businesses Overview
-
Textile
-
Businesses
- Textile
- Overview
- Markets
- Brands
- Expertise
- Media
- Contact Us
- Chemical
- Flooring
-
Performance Solutions by Milliken
-
Businesses
- Performance Solutions by Milliken
- Overview
- Consulting Services
- Education and Events
- Resources
- Virtual Tour
- Contact Us
- Products
-
Industries
-
Main Menu
- Industries
- Industries Overview
- Agriculture
- Apparel
- Automotive and Transportation
- Building, Construction, and Infrastructure
- Coatings, Paints, and Inks
- Commercial
- Consumer Goods
- Education
- Energy and Utilities
- Government and Defense
- Healthcare and Life Sciences
- Hospitality
- Manufacturing
- Packaging and Print
- Residential
- Sustainability
- Careers
Sacred Commitment to Health and Safety:
Lessons from Milliken's Safety Way
Health and safety are cornerstones of Performance Solutions by Milliken. Our long-standing dedication to these principles are seen through our in-house program, the Milliken Safety Way.
A Sacred Commitment.
Advancing health and safety as a way of life requires a “sacred” operational commitment to affect lasting change. This means all frontline staff are expected to dedicate time and energy to health and safety daily, in a space expressly set aside for committee gatherings.
No more corner of the company bulletin board or ad hoc breakroom sessions. Floor space is now reserved for meetings and measurement boards displaying the latest leading indicator results.
Sacred time and space are substantial company commitments. Is it worth it? “Safety isn’t free,” Houston states simply. Yet, as the Koop Award investment example shows, few expenditures have more certainty of return than health and safety. Here are a few recent examples of our engagements in action:
- FOOD AND BEVERAGE: A 400-employee plant achieved 100% health and safety subcommittee participation by all plant employees (hourly and salary) within a few months, along with a 63% reduction in hand injuries.
- PAPERBOARD AND PACKAGING: Health and safety dramatically improved across dozens of plant locations, with some reporting no incidents. Additional benefits included a 50% reduction in rework, an 80% decrease in waste, and a 60% decrease in equipment changeover times.
- CONSUMER PACKAGED GOODS: A health and safety focus helped achieve approximately $2 million in annualized savings through improved productivity, with five million safe work hours logged.
Milliken’s long-time dedication to its in-house health and safety program, called The Milliken Safety Way, illustrates another kind of outcome.
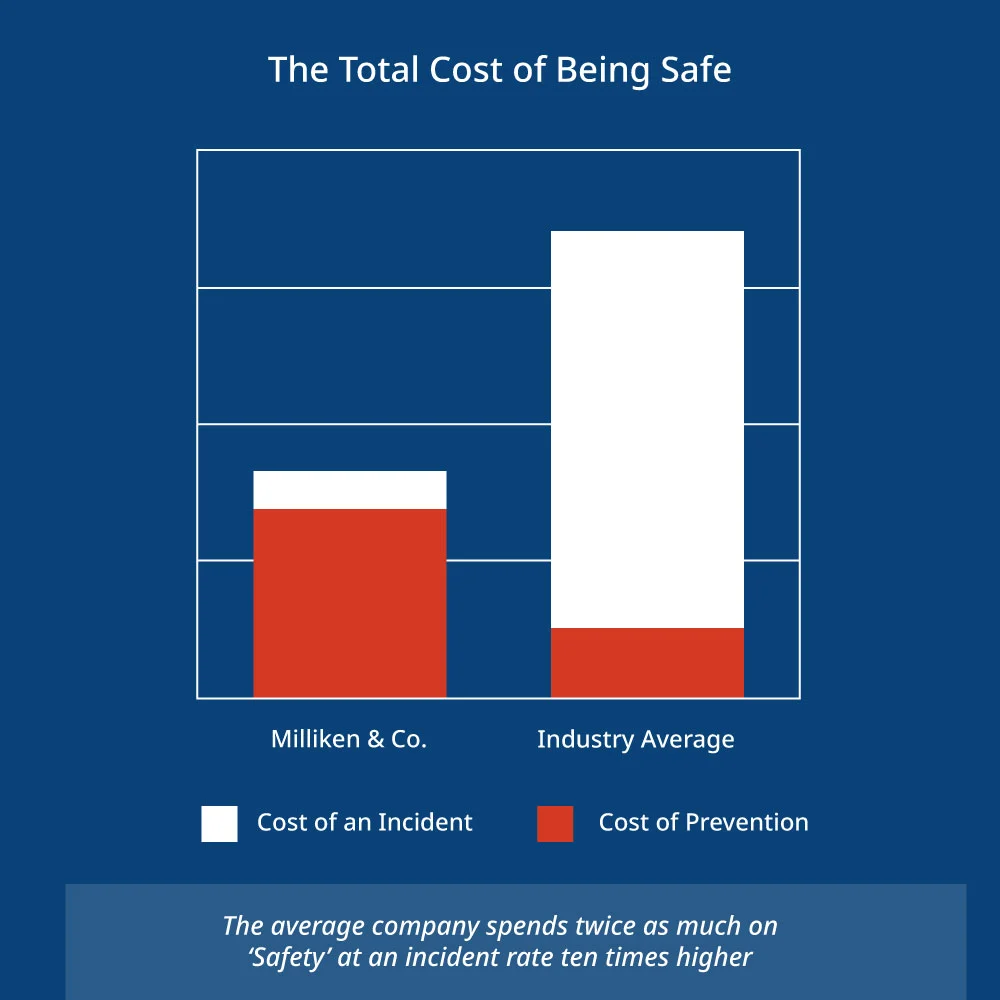
When Do You Invest?
Milliken’s aggressive investment in hazard prevention is offset by dramatically lower costs on the incident side, as this chart shows. Additionally, a health and safety culture fosters a more cohesive, integrated, and can-do workforce, accustomed to sustainable team-building and unified goal setting.
For Dede Ericson, Director of Client Engagement, and Scott Houston, a UK-based Senior Practitioner at Performance Solutions by Milliken (PSbyM), these intangible rewards are most impressive. Ericson, for example, notes, “The frontline folks don’t think about it in monetary terms. They live the results. They feel safer. They feel valued and protected by their line manager. As Milliken performance and health and safety practitioners, we must show a dollar return to management. But it’s a result we typically don’t discuss with frontline workers, unless instructed to do so.”
9 Health and Safety Culture Principles
Over 30 years of working with hundreds of companies worldwide have demonstrated the efficacy of The Milliken Safety Way, the embodiment of the organization’s hard-won health and safety lessons. These nine tenets have proven adaptable across all industries and engagements.
- Establish health and safety leadership in your plant.
- Design health and safety ownership into everyday life.
- Commit to a sacred time and place.
- Measure the right health and safety metrics.
- Give feedback the right way.
- Maintain constant focus on awareness activities.
- Make health and safety highly touchable.
- Present health and safety education for all.
- Define care management processes.
The Sound of an Unsafe Plant.
It could be a squeak, squeal, bang, or hiss. It’s the sound of something-isn’t-right. There’s danger around the corner.
For seasoned health and safety and performance practitioners like Ericson and Houston, a discordant machine noise piques ears trained by countless factory floor walk-throughs. “Safety is a proactive process,” Houston says. “If everything sounds, feels, and smells fine, you know the plant is probably 90% of the way there for safety.
“In plants with safety challenges, an odd sound, sight, or smell immediately puts you on alert for safety hazards.”
Partner With Us Today